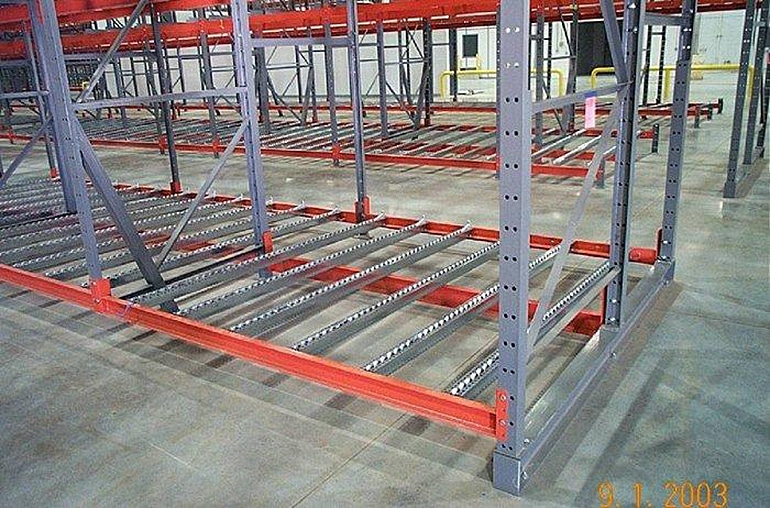
Wire Mesh Decking:
Wire decking creates a “floor” across the horizontal shelf beams, which helps support the stored items and prevents products from falling through the racks themselves.
Timber Decking:
Timber or wood decking fills a similar role to wire decking, but comes in two forms: slated close-boarded. Slatted wood decking forms rows of timber across the support beams, while close-boarded makes a wooden “floor” to the row of racking.